Revolutionizing Design Advanced Techniques in Liquid Silicone Rubber Molding
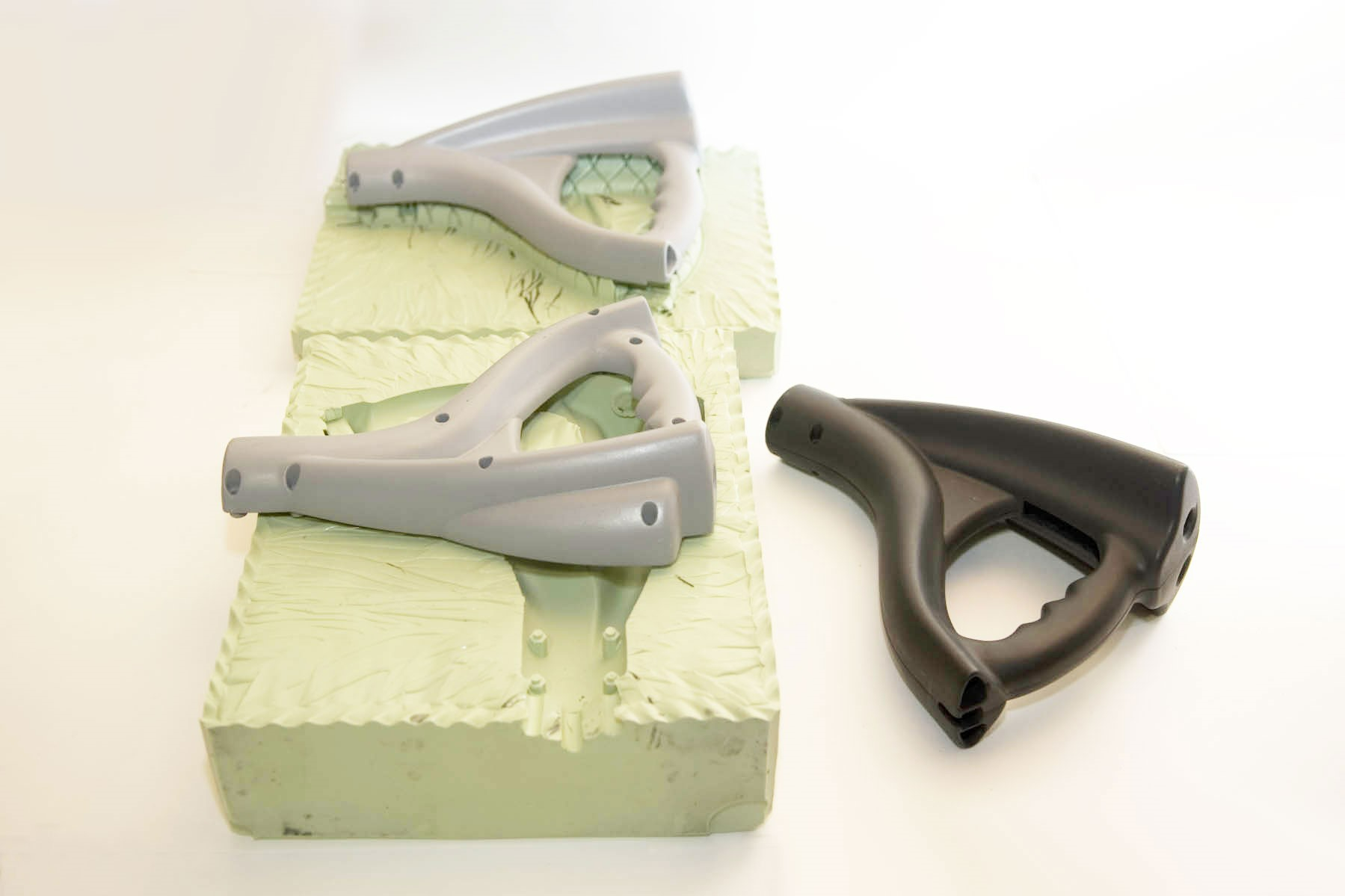
In the world of manufacturing, innovation is a constant driving force, and the techniques used in liquid silicone rubber (LSR) molding have undergone remarkable advancements in recent years. Liquid silicone rubber molding, a process that involves injecting liquid silicone into a mold to create highly precise and flexible parts, has become a pivotal technology in industries ranging from automotive to medical devices. The latest advancements in LSR molding are not only enhancing design capabilities but also setting new standards for efficiency and quality.
Cutting-Edge Techniques Enhancing Precision
One of the most significant developments in LSR molding is the refinement of precision techniques. Modern Liquid Silicone Rubber Molding machines are equipped with advanced control systems that allow for greater accuracy in the injection process. These systems use real-time data to adjust parameters such as pressure, temperature, and injection speed, ensuring that every part produced meets exact specifications. This level of precision is particularly crucial in applications where even the slightest deviation can lead to product failure or safety issues, such as in medical devices and high-performance automotive components.
Enhanced Material Properties through Innovation
Recent advancements have also focused on improving the material properties of LSR. New formulations of silicone rubber are being developed to offer enhanced durability, flexibility, and resistance to extreme temperatures and chemicals. These innovations allow manufacturers to design parts that perform better and last longer, even in harsh environments. For instance, the development of self-healing LSRs and those with antimicrobial properties is opening up new possibilities in healthcare and consumer goods.
Streamlining Production with Automation
Automation is playing a crucial role in the evolution of LSR molding. The integration of robotic systems and automated handling equipment has streamlined production processes, reducing manual labor and minimizing the risk of human error. Automated systems can perform tasks such as part removal, inspection, and packaging with high speed and consistency, leading to increased productivity and lower production costs. Additionally, automation allows for more flexible production runs, enabling manufacturers to quickly adapt to changing market demands.
Sustainable Practices in LSR Molding
As industries increasingly focus on sustainability, LSR molding techniques are also evolving to meet environmental standards. Advances in recycling processes and the development of more eco-friendly silicone formulations are helping to reduce the environmental impact of LSR production. Manufacturers are now able to recycle silicone waste and use it in new products, contributing to a circular economy and minimizing waste.
Future Prospects and Applications
The future of LSR molding holds exciting possibilities. With ongoing research and development, we can expect even more innovative techniques that push the boundaries of what is possible with silicone rubber. Emerging applications in fields such as wearable technology, advanced robotics, and personalized medicine suggest that LSR molding will continue to be a key technology in the creation of high-performance, custom-designed components.
The advancements in liquid silicone rubber molding represent a significant leap forward in manufacturing technology. With improved precision, enhanced material properties, streamlined production processes, and a focus on sustainability, LSR molding is poised to revolutionize design across various industries. As these techniques continue to evolve, they will undoubtedly unlock new opportunities for innovation and excellence in product design.