Transforming Metal the Evolution and Impact of Pressure Die Casting Technology
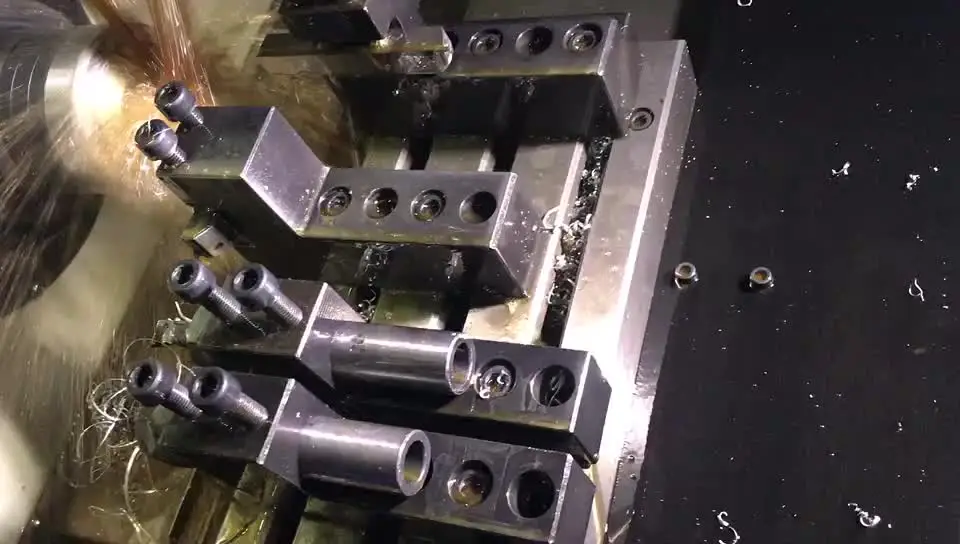
Metal casting is one of the oldest and most essential manufacturing processes in human history. Among the various methods used to mold metals into desired shapes, pressure die casting has emerged as a transformative technology. This article explores the evolution of pressure die casting, its technological advancements, and the significant impact it has had on industries worldwide.
The Origins of Die Casting
Die casting can be traced back to the 19th century when it was first developed for the printing industry. The need for durable, high-precision metal typefaces led to the creation of early die casting machines. The first patented die casting process was granted in 1849 to Sturges for creating movable type for printing presses. This early process laid the foundation for modern Pressure Die Casting by demonstrating the viability of using pressure to force molten metal into molds.
Evolution of Pressure Die Casting Technology
The initial die casting process was limited by the types of metals it could work with and the precision of the molds. However, as industrial demands grew, so did the technology. The introduction of zinc and aluminum alloys in the early 20th century marked a significant advancement. These metals offered a better balance of strength, weight, and malleability, which made them ideal for die casting.
World War II played a crucial role in furthering die casting technology. The need for mass production of military components, coupled with the scarcity of certain materials, pushed the development of more efficient and versatile die casting methods. By the mid-20th century, pressure die casting had become a mainstay in industries like automotive, aerospace, and consumer electronics.
How Pressure Die Casting Works
Pressure die casting involves forcing molten metal into a steel mold, or die, under high pressure. The process typically consists of four main steps:
Preparation of the Die: The mold is prepared by coating it with a lubricant to ease the release of the cast part and to extend the mold’s life.
Injection: Molten metal is injected into the die at high pressure, filling every cavity and detail of the mold.
Cooling: The metal cools and solidifies quickly due to the mold’s conductive properties.
Ejection: Once solidified, the die opens, and the cast part is ejected.
This process allows for the production of complex shapes with high accuracy and repeatability, making it ideal for large-scale manufacturing.
The Impact of Pressure Die Casting on Industry
Pressure die casting has revolutionized manufacturing across multiple sectors. In the automotive industry, it has enabled the production of lightweight, high-strength components essential for improving fuel efficiency and reducing emissions. Complex engine parts, transmission housings, and structural elements are now commonly produced through this method.
In the consumer electronics industry, die casting allows for the creation of intricate and durable casings for devices like smartphones, laptops, and cameras. The ability to produce thin-walled, high-precision parts has been instrumental in the miniaturization and performance enhancement of these devices.
The aerospace industry has also benefited from pressure die casting, particularly in the production of components that require both strength and low weight, such as turbine blades and airframe structures. The precision and consistency of die casting ensure that these critical parts meet stringent safety and performance standards.